How long does it take to modernize an elevator?
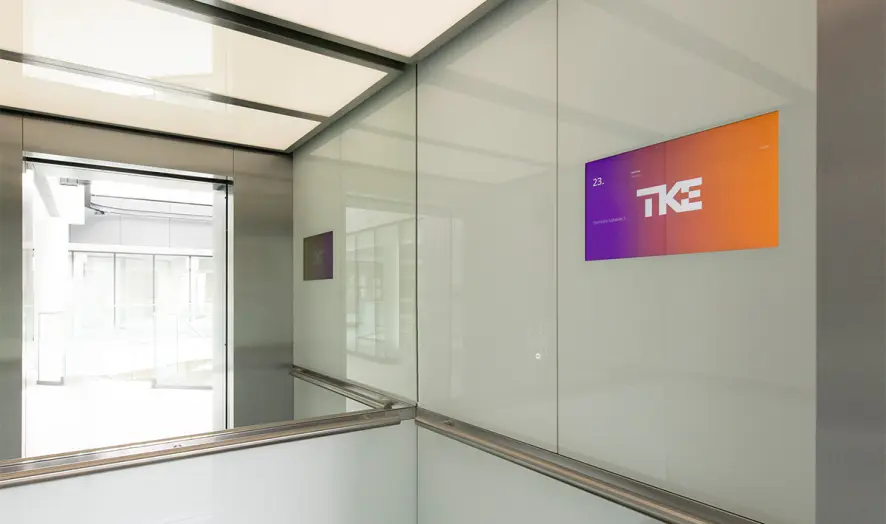
Elevator modernization is vital for building managers and operators who aim to keep their properties safe, reliable, and efficient. As technology evolves, older elevators can become a bottleneck that inhibits visitor flow through a building. In addition, elevator breakdowns may become more frequent, and procuring suitable spare parts becomes more challenging.
At this point, many building operators start thinking about elevator modernization, and one factor that is central to this consideration is the question: How long does it take to modernize an elevator?
Unfortunately, there is no single answer to this complex question, and depending on factors such as the scope of the modernization work, the height of the building, etc., elevator modernization work may take up just a few weeks, or up to several months. In this article, we go through all the factors determining the length of the modernization work.
General Guidance on How Long It May Take to Modernize an Elevator
The duration of an elevator modernization project varies depending on the scope of work and the condition of the existing system. Targeted upgrades of specific components—such as replacing control panels, drive systems, or worn mechanical components—can often be completed within a few weeks, minimizing service disruptions.
However, more extensive modernization efforts that involve major structural modifications, electrical system upgrades, or full cabin replacements may extend across several months. The timeline is influenced by factors such as building constraints, regulatory compliance, and the desired performance enhancements of the modernized installation.
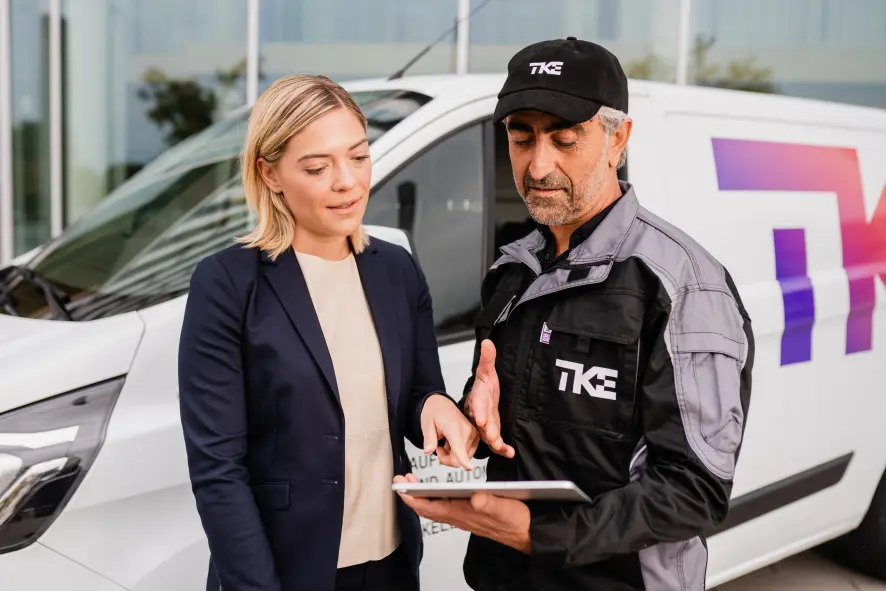
Factors That Impact the Time Required to Upgrade Elevator Systems
There are numerous factors that can either accelerate or prolong the time it takes to modernize an elevator. One of the most important ones is the scope of the modernization work.
Full Elevator Replacement vs Partial Elevator Modernization
Modernizing an elevator can range from a partial upgrade of a specific component to a full replacement. Naturally, the former will take much longer than the latter. Full replacements do not require long downtimes, but they can also affect other parts of the building as bulky components need to be transported through building entrances and lobbies. Also, depending on the number of elevators available, a several-month-long service disruption is likely highly taxing on building tenants and visitors. A partial elevator modernization, on the other hand, typically leaves the basic elevator structure and most mechanical elements intact while focusing only on replacing specific components such as controls, motors, or door mechanisms to eliminate causes of past performance outages (or to improve elevator efficiency). The more narrowly defined the scope, the easier it is to fit upgrades into a tighter schedule.
While each approach has its advantages, we would generally advise thinking of elevator modernization as an ongoing process rather than a one-time fix. So, rather than attempting to resolve all issues in one go and to face long downtimes that also require significant capital expenditures, it is often more effective to develop a longer-term modernization strategy that minimizes investment requirements, as well as extended periods with elevator outages. Feel free to get in touch with our elevator experts in India to determine the most efficient modernization strategy for your elevators.
The Type of Elevator That is Being Modernized
Different types of elevators have distinct modernization requirements that can influence how long a project takes. Hydraulic elevators, for instance, use fluid-driven pistons to move the elevator car, whereas traction systems rely on hoist ropes, counterweights, and a motor.
Modernizing mechanical parts of both systems is an entirely different processes that have different time requirements.
Modernizing a hydraulic lift may require refurbishing or replacing the pump unit, fixing leaking seals, or reinforcing the piston. In theory, hydraulic elevators have fewer mechanical components, which can help speed up the modernization process..
In practice, however, traction elevators are becoming the predominant system, as they are more energy efficient, better suited to service higher buildings, and can transport heavier loads. Modernizing a hydraulic elevator by replacing it with a traction elevator does therefore often require a substantial amount of time.
How Building Height Impacts Elevator Modernization
A building’s height may or may not impact the modernization timeline. If only electrical parts are being renewed or if engine parts are being replaced, then the height of a building can have zero to no impact on the modernization schedule. If, however, more comprehensive modernization work is carried out, the building height can have a considerable influence on the complexity of an elevator modernization and the time requirements. High-rise structures, especially those spanning dozens of floors, introduce logistical challenges that mid-rise or low-rise buildings generally do not face. Moving large components to the top of a tall building may require specialized hoisting equipment, which needs to be set up. Also, the higher an elevator travels and the faster the travel speed, the more comprehensive the safety systems. This often requires additional safety testing once the modernization work is complete.
In high-rise buildings with many tenants, scheduling work can also be more complex. The impact on many stakeholders needs to be carefully weighed, especially for commercial buildings, which often have strict guidelines with regard to working hours during which engineering tasks can be carried out.
This is why many building managers prefer a phased approach (as outlined above), where modernization work is carried out car by car and component by component. Such a coordinated approach reduces overall disruptions as well as immediate capital requirements.
Access to a Building
Building access is another key variable that can either streamline or complicate an elevator modernization project. This point is particularly relevant for full replacements. Not only do contractors and technicians need access to elevators, but spare parts and heavy equipment need to be transported as well.
If a property lacks a nearby loading area or if interior corridors are narrow, this can slow the movement of materials. Certain properties also enforce strict security measures that require contractors to follow specific check-in procedures or restrict the hours during which work can take place. These hurdles can stretch out the project’s duration, even if the modernization work itself is relatively straightforward.
Arranging for dedicated loading zones and agreeing on practical working schedules and access procedures can ultimately be beneficial for all parties involved as tenants regain access to fully functional elevators as quickly as possible, while building operators minimize operational impact. Good communication and organization are thus important to reduce the risk of delays tied to logistics and access, ultimately saving both time and resources.
Regulatory Approvals & Safety Compliance
Specific building codes that govern elevator modernizations can have an impact on the time it takes to complete a project. Depending on the legislative framework and the type of building, government-mandated safety testing and inspections may need to be carried out. Scheduling inspections and applying for permits in due time helps smooth this process and helps reduce waiting times that could otherwise cause project delays. At TKE, we are very familiar with federal as well as state-level safety requirements in India and incorporate these in all elevator modernization project plans.
Elevator Modernization Project Management Tips
Breaking an elevator modernization project into different phases is key to not only mitigating disruptions but also extending the overall lifespan of an elevator system. Iteratively modernizing critical components, going car by car, prevents major breakdowns as parts are being replaced before they reach their end-of-life stage, or before spare parts required to repair them become unavailable. This phased approach with clearly defined milestones also helps Indian building managers control maintenance costs while keeping elevators operating efficiently.
This is why building operators in India find that working with an experienced elevator services provider such as TKE is the ideal approach to manage modernization projects. Our elevator specialists bring in-depth knowledge about modernization best practices, not only about TKE elevators, but about elevators manufactured by any other brand. As an engineering company, we are well-versed in designing custom solutions that meet your specific requirements and goals and often also shorten the overall timeline required to complete modernization work. Contact our nearest branch in India to learn how we can best support you.