Elevating the Modernization Game: Why it’s never too early to think about updating your elevator
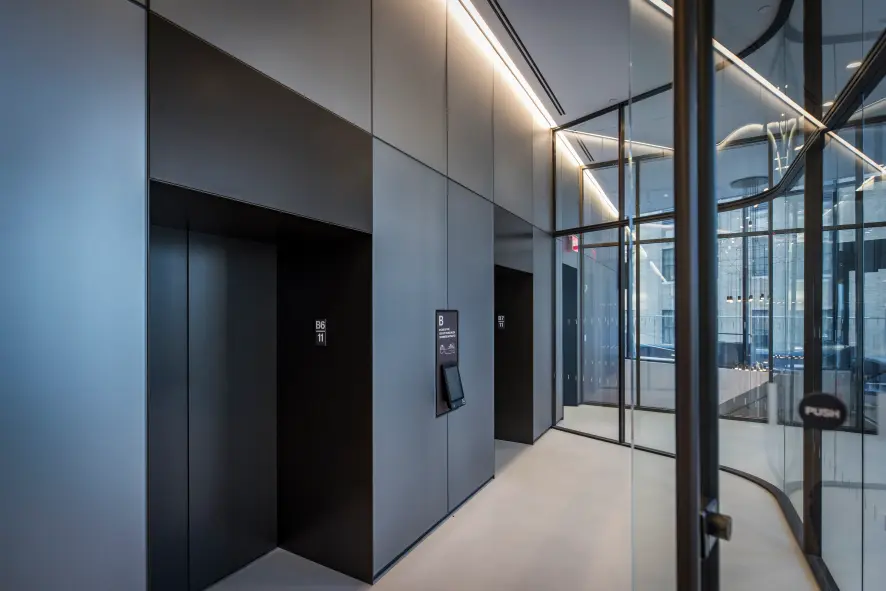
The life cycle of an elevator is approximately 30 years, making modernization critical to millions of people riding elevators every day. An elevator modernization replaces your equipment’s critical components, making it look and perform like new.
More than 30% of the world’s 21 million elevators are more than 20 years old making elevator modernization critical to building safety and the growth of urban communities around the globe.
"There are more than 1 million elevators in the United States, and thousands of them require modernization every year," says VP of Modernization Sales, Andrew Stein. “Upgrading elevators is essential to maintaining efficiency, safety and aesthetics. We sell elevator modernization in two primary ways – through RFPs (requests for proposal).
With RFPs, a building owner determines – sometimes with the help of a consultant – that their elevators have reached a certain age, its tenant population is shifting or its footprint is evolving, necessitating an upgrade in some capacity. "On these projects, especially if it's a significant modernization, they work with the consultant to administer a bid process that companies [like TK Elevator] respond to," says Stein.
The second route is when sales teams start the modernization discussions with customers early. A unit's age and its components' potential obsolescence are some of the biggest factors in building owners deciding to modernize, and providing this information early is crucial.
"A lot of what drives interest in modernization is customers are facing aging equipment, obsolete components, and operational concerns – in older elevators when an elevator goes down, it stays down longer," says Daniel Gross, Area Sales Director for the Southeast region.
TK Elevator recently declared TAC-20, its former hydraulic controller package, obsolete, and prior to that – a couple years ago – the company declared the Dover DMC controller package obsolete. "So our sales reps turn to customers with all those units and say, 'Hey, your unit is 25 years old and no longer supported by parts and components needed for repairs or replacement, and you need to think about modernizing,'" says Stein. "Because what inevitably will happen is the next time the elevator shuts down, we won't be able to return it to service quickly or – in some cases – at all."
Out-of-service elevators are the bane of building owners, managers, and, of course, tenants, so while modernizing and updating elevators have a lot of appeal, it often requires a significant financial investment.
"Our goal is to make elevator modernization accessible and financially manageable for our customers," says Gross.
TKE works with customers to customize flexible payment options such as a 25 or 50 percent initial down payment, with the remainder of payments once the work begins. "We also educate building owners about the long-term benefits to modernizing – lower energy costs, shorter wait times for tenants and users, and shorter service times when our technicians come out," says Gross.
Additionally, TKE sales reps inform customers of any local, state, or federal incentives available for modernizing. For example, upgrading elevators in older buildings can contribute to LEED certification that may qualify for tax breaks. In the long run, modernization is not just an upgrade, it's a strategic investment in efficiency, sustainability and enduring value.
Click here to learn more about our modernization packages for your hydraulic and traction elevators: Elevator Modernization by TK Elevator | US