Sustainability: It’s Inside Our Elevators
Global businesses and governments increasingly recognize the responsibility for sustainable development. Climate change and resource management pose the greatest long-term threats to our future. This makes sustainability not only a social responsibility but, according to a Harvard Business School Insights Blog, an essential business strategy.
The Environmental Protection Agency’s Strategic Plan identifies the built environment as a key priority area for sustainable materials management. The EPA report identifies the rapidly increasing consumption of industrial materials to construct, maintain, and operate the built environment. It demonstrates how “the extraction, transportation, use and disposal of these materials result in substantial environmental impacts, including emissions to the air, water and land; energy and petroleum consumption; use of non-renewable mineral resources, expenditure of fresh water, and land and habitat use.”
We at TK Elevator recognize the critical role we play in moving people through the built environment. That’s why we strive to create more sustainable products and to be transparent about our ecological impact.
Setting a Precedent for Our Industry
In 2014, TK Elevator set a new precedent for our industry by developing a health product declaration (HPD) or “ingredient list” of all the materials that make up our elevator cabs. This was a gargantuan task given the 10,000+ separate parts in an elevator system.
An HPD is an impartial tool used to formally document and disclose a product's material content. It enables manufacturers to present product information in a consistent, transparent and easy to understand format. The goal of our HPD was to help customers make better-informed decisions, especially at a time when architects, specifiers and building owners were beginning to require sustainability commitments to bid on projects. In October 2013, 24 major architecture firms took a stance on transparency and issued letters formally requesting HPDs, environmental product declarations (EPDs), or other forms of material content disclosure. For some firms, failure to comply meant manufacturers lost preference.
When asked about the project, Senior Sustainability Manager Monica Miller Brown remarked, “We were the first in our industry to pursue this level of transparency and one of the first manufacturers to develop an HPD for a product as complex as an elevator system. We remain alone in our industry as a built-environment leader in transparency.” Miller Brown noted that many manufacturers of building materials pursuing an HPD don’t make products as complex as an elevator: “Carpet, wall covering and paint have fewer parts, and so the process is simpler. We set a precedent for other manufacturers of complex building products.”
The team spent over a year collecting and analyzing data from bills of materials (BOM) and drawings. A sustainability coordinator traveled to the factory to research the scope, reviewing the materials in each of the elevator factory’s sections. They then reached out to hundreds of suppliers to gain more insight into the product makeup for a full Health Product Declaration publication for our elevator cabs in support of the endura MRL launch. Collaborating with the factory, the sustainability team broke down the elevator cab, organized the data and detailed the basic material components and then reorganized and populated those elements into the HPD building tool.
The sustainability team then went on to seek a full Material Health Certification from the Cradle to Cradle Products Innovation Institute for both our cab and for our enviromax® product. Our Bronze certification took the HPD one step further and is not only transparent—but ensures thr product contains no worst-in-class chemicals and is safe for use. Our enviromax® Material Health Certificate was the first Platinum Material Health Certificate awarded, providing it is a fully optimized product from a health perspective.
enviromax®: Continuing our Sustainable Legacy
Today, TK Elevator continues to move beyond the industry standard for sustainability. Since 1937, our hydraulic elevator system has been the standard for energy efficiency and reliable cost-saving operation. Now we know efficient elevators save environmental costs as well. Our 95% petroleum-free endura elevators exceed the demands of today’s low-rise buildings as smooth, quiet and efficient workhorses.
Traditional hydraulic elevators rely on petroleum-based fluid to operate, possibly exposing users to groundwater contamination, soil remediation and a reliance on non-renewable resources. When TK Elevator partnered with BioBlend Renewable Resources to develop enviromax®, the elevator industry’s first performance-improving, plant-based hydraulic elevator fluid, we created a new industry precedent for sustainability.
Enviromax®-equipped elevators perform better and do it without petroleum fluids or heavy metal additives. Formulated from renewable and biodegradable high oleic natural esters (HONEs), enviromax® scored well above government toxicity standards when tested at an independent laboratory.
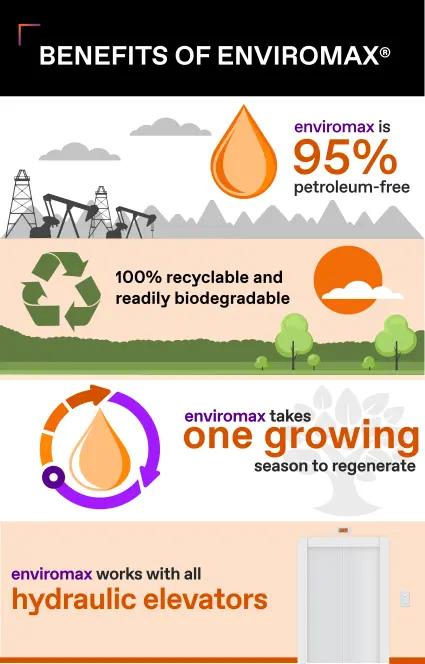
Plant-based enviromax® is readily biodegradable, 95% free of petroleum and 100% recyclable. It exceeds the highest standards for biodegradability, and it takes only one growing season to produce the oils for the product. This is in stark contrast to the tens of thousands of years required for petroleum-based fluid, and it can be easily recycled and reused in a variety of products. enviromax® works with old or new hydraulic elevators, whether made by TKE or not. It can improve the efficiency and ride quality of your elevator with more stability through load and temperature ranges and can increase key sustainability metrics for your building. If you have questions about upgrading to enviromax®, contact a nearby sales representative.